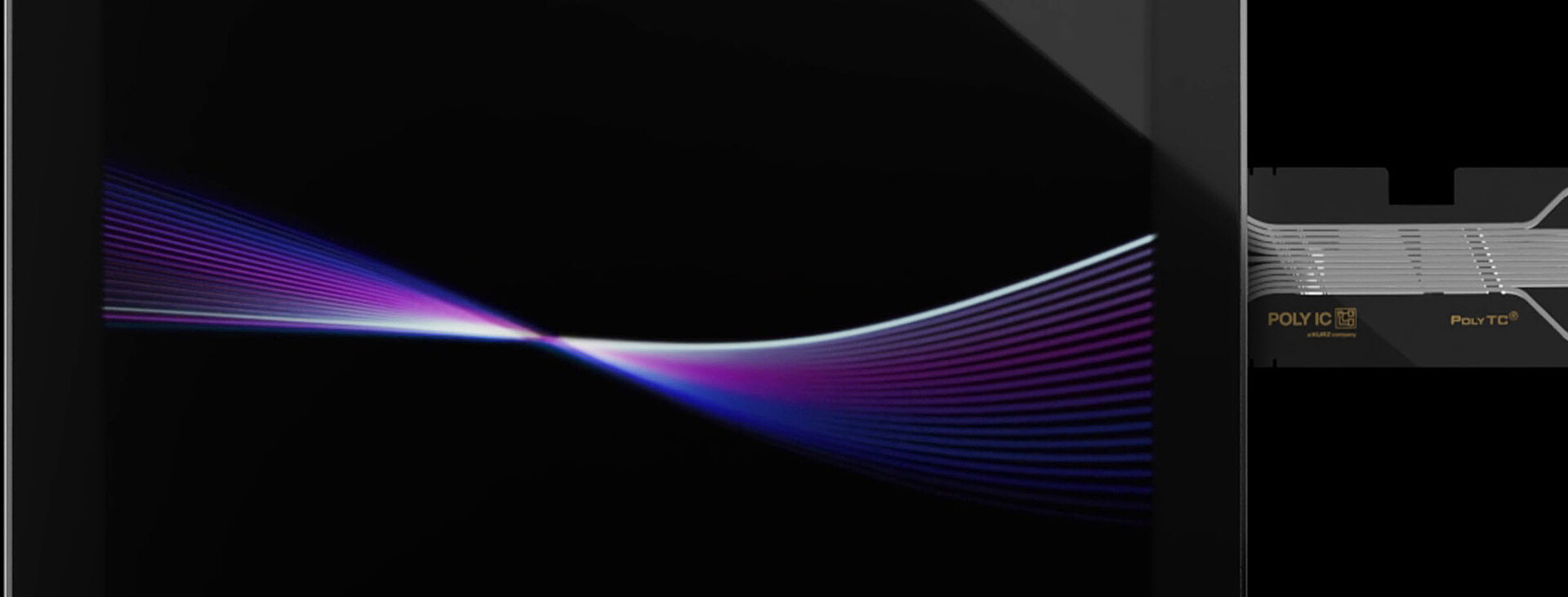
Display stacks with IMD and touch functionality
A versatile alternative to glass displays
A collaborative project between KURZ, POLYIC, and Elektrobit
High-quality HMI (Human-Machine Interface) solutions and displays with touch functionality are on trend. Not least due to increasingly powerful smartphones, consumers also expect reliable, smooth operation and a brilliant display in other areas of their everyday lives. At the same time, there is increasing cost pressure.
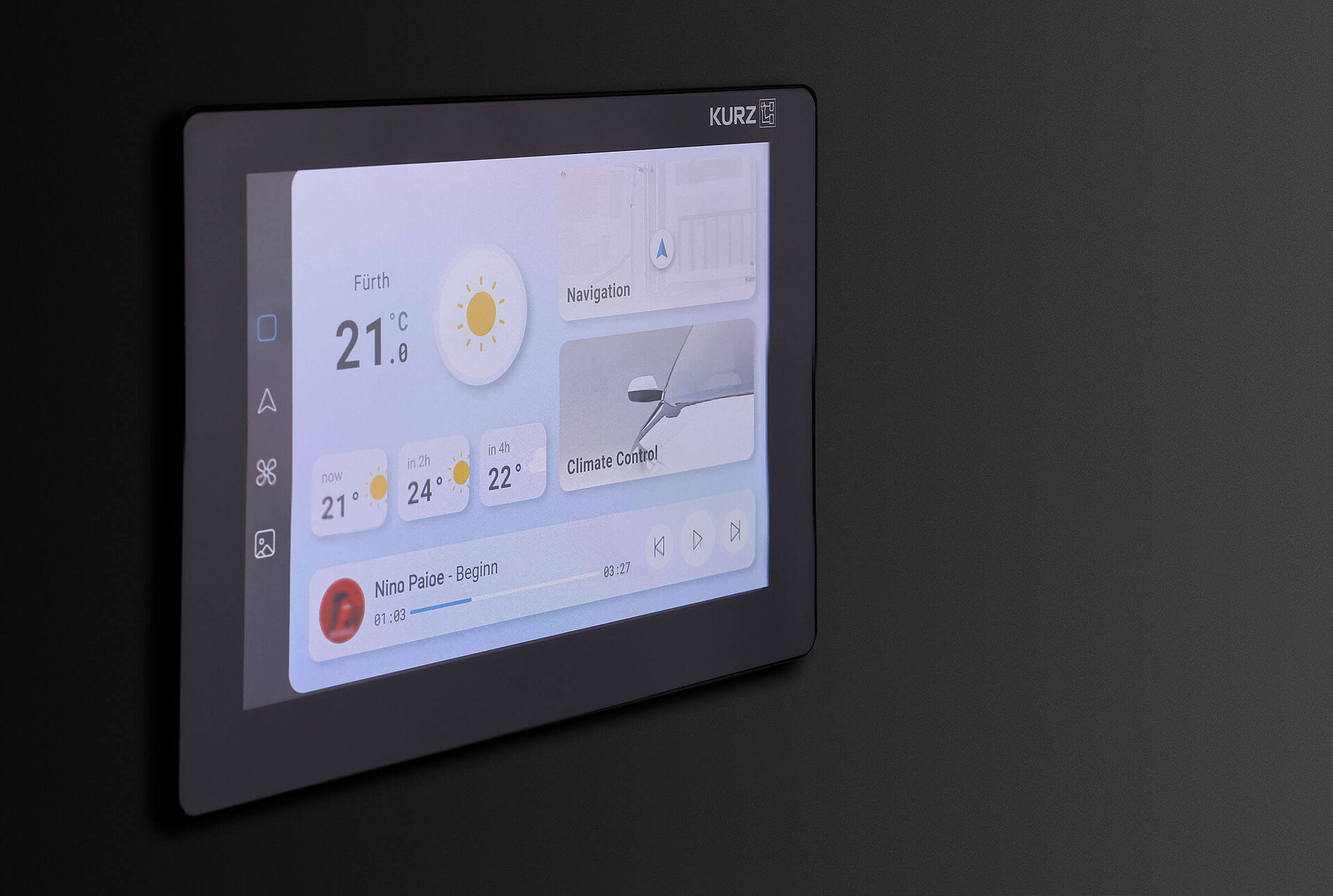
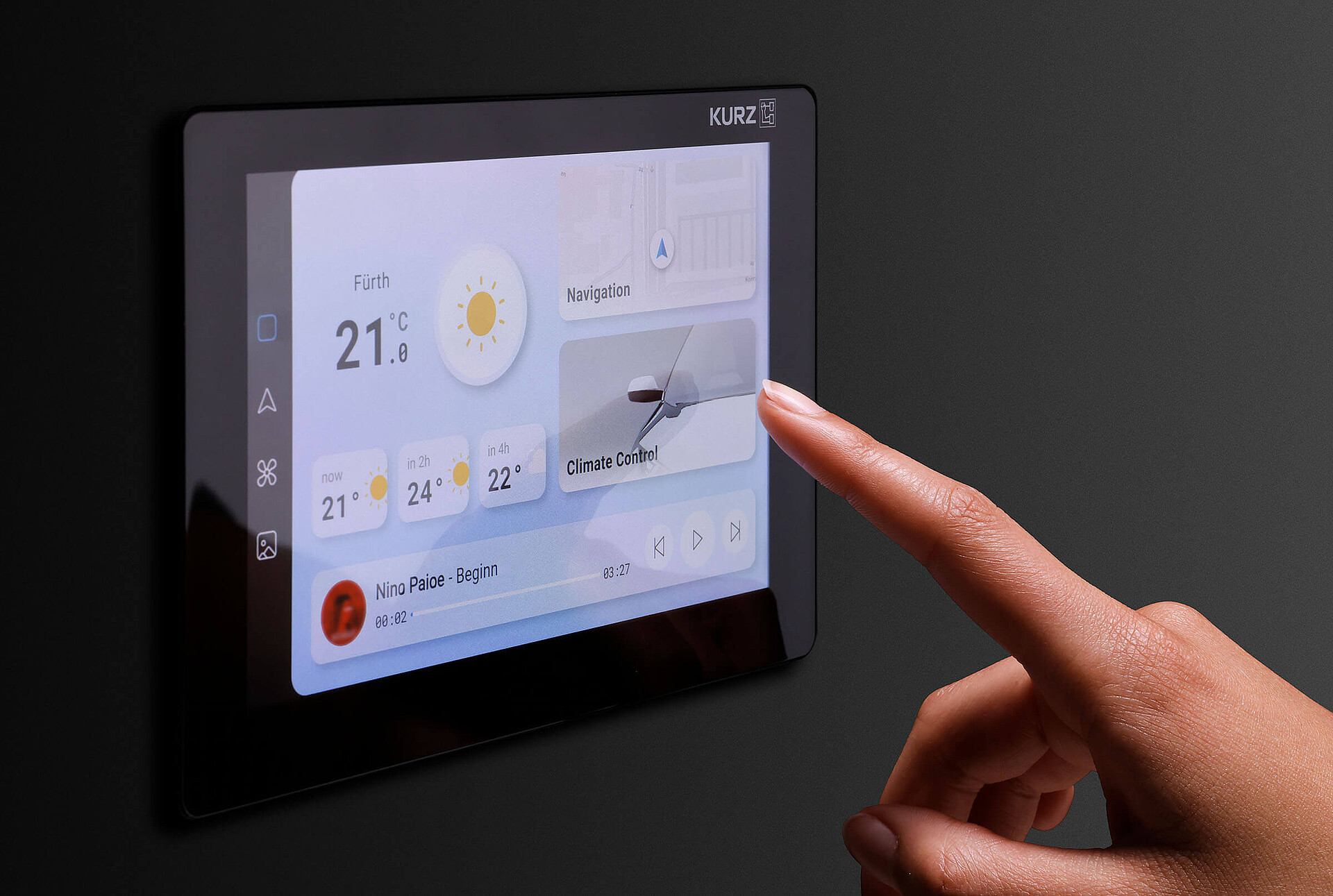
The challenge
There is an urgent need for efficient processes that save time, money, energy, and resources in the production and decoration of displays. However, manufacturers should not have to compromise on design. Seamless, closed surfaces - even for curved components - as well as a wide range of decoration options and sustainable production are in demand.
The goal
As part of an ambitious project, LEONHARD KURZ set itself the goal of developing a more cost-effective alternative to high-priced glass panels, which can also be used in series production beyond the luxury segment. The company was looking for a solution that could be adapted to different budgets, but that still focused on high quality. Various demonstrating devices were also used to visually show the optical properties of a variety of possible display stacks. In order to be able to compare subjective impressions with objective values, all relevant optical parameters for the display stacks were measured. Also on board: KURZ subsidiary POLYIC, an expert in advanced sensor technology, and the Ulm branch of Elektrobit, an award-winning global provider of embedded software and automotive display experts.
The solution
Instead of expensive glass panels, the cooperation partners opted for plastic displays, which are more cost-effective to produce thanks to efficient technologies. Different variants were produced in which the touch sensors are laminated. Alternatively, it is also possible to inject the sensors. Touch operation is possible with all versions, just like with conventional glass displays. The panel of these display stacks is manufactured and coated by KURZ using the IMD (In-Mold Decoration) process, with polycarbonate (PC) as the panel material in injection molding. PolyTC® sensors from KURZ subsidiary POLYIC and, in some cases, other optical filter foils are integrated on the back of the display.
The demonstrating devices produced show, among other things, the different coating options for the panel surface, which can vary depending on requirements and budget. Surfaces with reduced light reflection or antibacterial and antiviral coatings using KURZ BIOFENSE® are possible, for example. In addition, various sensors based on PolyTC® metal mesh technology are available. These have different optical properties and thus also distinguish themselves in terms of manufacturing costs. A process is now used in series production that drastically reduces the reflection of the silver structures on the sensors. The grid-like silver structures are responsible for electric conductivity with maximum mechanical flexibility and enable the use of sensor technology even in designs with certain 3D shapes.
The display stacks also differ considerably in terms of design, as there are different design options for each of the built-in layers - from the coating of the front screen to the touch sensors and the type of connection between the touch screen and display. For example, the best visual variant is one in which the screen and display are bonded together via optical bonding. Although the LOCA (Liquid Optical Clear Adhesive) method used here is more expensive than alternative methods, it has a decisive advantage: There is no air gap between the touch screen and the display, which avoids light refraction and annoying reflections in display stacks with an air gap. The display stacks manufactured using the LOCA process retain their full brilliance and are, therefore, also ideally suitable for use in bright environments.
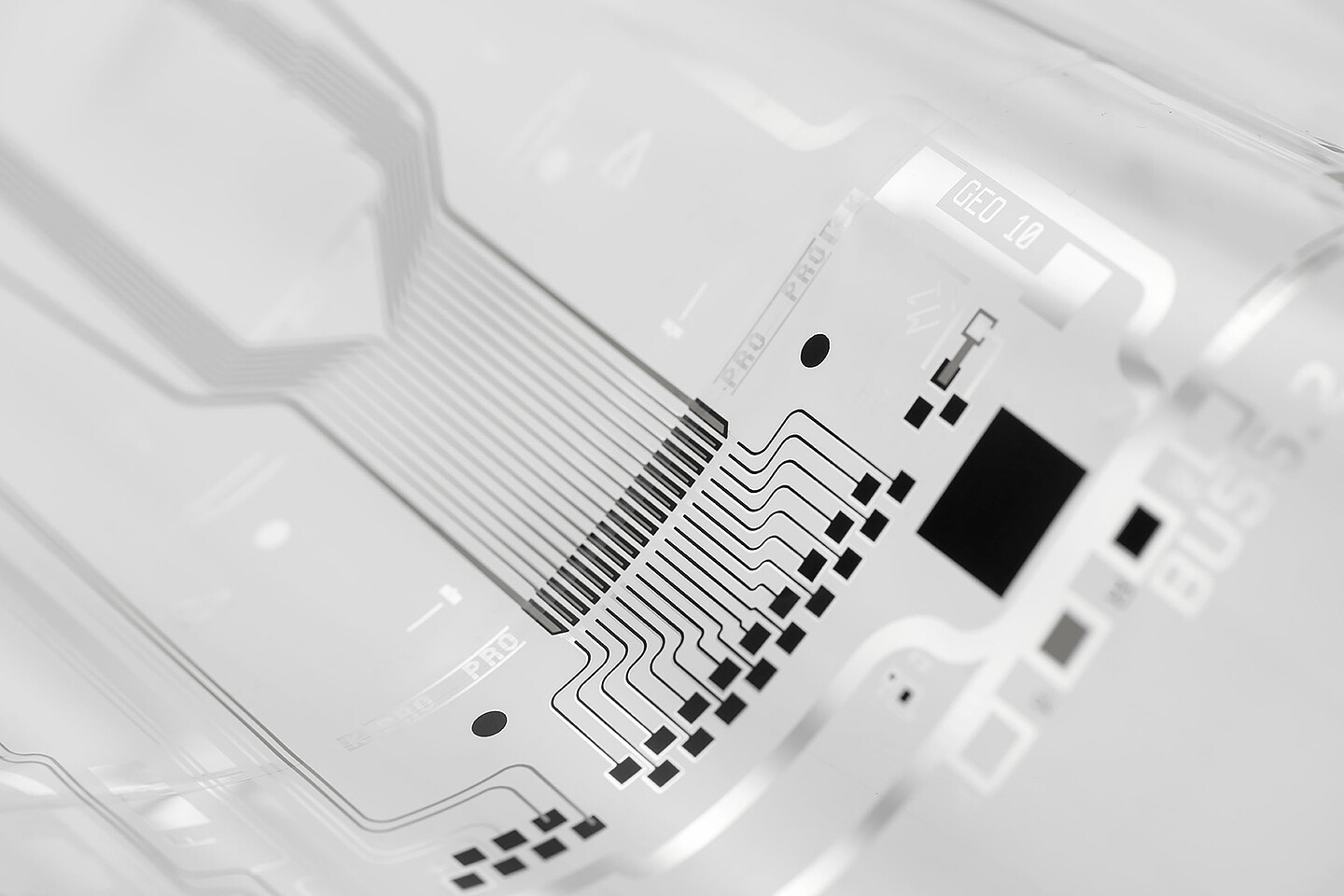
POLYIC: Supplier of durable, conductive, transparent and secure sensors
The sensors of the KURZ subsidiary POLYIC are ‘made in Germany’ and meet the standards and requirements of many premium manufacturers. The unique PolyTC® technology is a cornerstone of POLYIC’s worldwide success and makes it possible to integrate very thin, flexible, and transparent touch sensors into a wide range of display applications. In addition to functionality, great importance is attached to the most diverse design aspects possible. The sensors are therefore ideally qualified for series production in several branches of industry. PolyTC® sensors impress with four advantages:
Durability. The sensors pass the tough endurance tests required by the automotive industry.
Conductivity. The highly conductive structure ensures that the sensors can be read especially quickly by the touch controller ICs, while having an outstanding signal-to-noise ratio (SNR). In addition to strong touch performance, this also facilitates applications with touch sensors behind thick materials.
Flexibility. The special structure of layers and the conductive structures make sensors very flexible, so they smoothly adapt to curved geometries as well.
Transparency. The PolyTC® sensors allow transparent or semi-transparent (radiolucent) touch applications. In contrast to the widely used ITO technology, which causes color shifts, they are also visually color neutral.
Why KURZ is the right technology partner:
- KURZ offers extensive expertise and in-depth experience in the automotive sector in compliance with stringent industry standards
- Through a network of subsidiaries and strong partners, KURZ bundles a great deal of expertise in various areas
- The combination of modern processes leads to design and functional solutions for series production
- KURZ is actively shaping change in many industries through innovative and sustainable technologies
- The company develops innovative decorations that don’t impair the recyclability of components, as well as durable components with self-healing surfaces
- KURZ continuously develops its processes and has more than 3,100 patented and patent-pending technologies
- KURZ is the world leader in surface finishing and produces under uniform quality and environmental standards in Europe, Asia, and the USA
- The combination of modern processes leads to design and functional solutions for series production
- As a 360° solution partner, KURZ delivers machines, tools, processes, technologies, and innovative designs from a single source
Conclusion
Thanks to In-Mold Decoration and other efficient processes, the new plastic displays from KURZ and POLYIC reduce production costs compared to expensive glass displays while offering the many advantages of plastic. They are not only ideal for series production but also open up numerous design possibilities. Among other things, smooth, homogeneous, and continuous surfaces can also be created on curved components, which can be decorated sustainably and in a high quality.