
HMI Overhead Light Console
LEONHARD KURZ creates an innovative HMI Overhead Light Console with strong technology partners via CO2-reduced In-Mold Electronics (IME) process.
The challenge
Vehicle interiors are set to become futuristic feel-good areas. Thanks to state-of-the-art technology and sophisticated decoration concepts, any surface can now be functionally equipped. Individually adaptable operation and a pleasant ambiance are important for end users - but so is the efficient, sustainable production of a component. KURZ develops solutions together with competent partners. One example is the Overhead Light Console, which was created in cooperation with injection molding machine manufacturer Wittmann Battenfeld, plastics specialist and manufacturer of complex plastic components Syntech Plastics, lighting expert ams Osram Automotive Lighting Systems (AMLS), and KURZ subsidiaries POLYIC and BAIER.
The roof-lining module is produced, decorated, and equipped with sensors in a single work step using the IMD process. It is characterized by its seamless, fully closed, 3D-shaped surface with integrated touch operation. Thanks to In-Mold Electronics, various functions such as the ambient light, reading light, and sliding roof can be controlled. To top it off, virtually all features can be individually adjusted. The integrated light projection makes it possible to display information or animations on different surfaces inside the vehicle. Recycled materials can be used for the component and deliver the same excellent production results as new material. It is fully recyclable, including the integrated touch sensors.
The goal
Design, function, and sustainability - manufacturers and suppliers must deliver this triad in order to stay competitive. KURZ and its technology partners have succeeded in bundling several production steps in a single process. This one-step process was the basic specification for this component. There are several advantages for car manufacturers: On the one hand, they save resources; on the other hand, the IMD process with simultaneous functional in-mold labeling - also known as In-Mold Electronics (IME) - allows custom decorations. A wide range of surface looks, through to technical designs and soft-touch effects, can be realized.
The solution
The concept component demonstrates several pioneering technologies that are already suitable for series production. Among other things, it shows which types of sensors can be integrated into an interior module: In addition to five capacitive touch sensors with haptic feedback, a touch slider has been integrated to control the ambient and reading light. The wafer-thin, highly transparent sensors are fully illuminated in the direct field of vision of the LED light surfaces, and function as individually assignable operating elements. Thanks to the shy tech design, the concept component only reveals its secrets at a second glance - the light structures in the decor are generally invisible. However, if, for example, there is an incoming call, they light up in accordance with the selected ambient lighting.
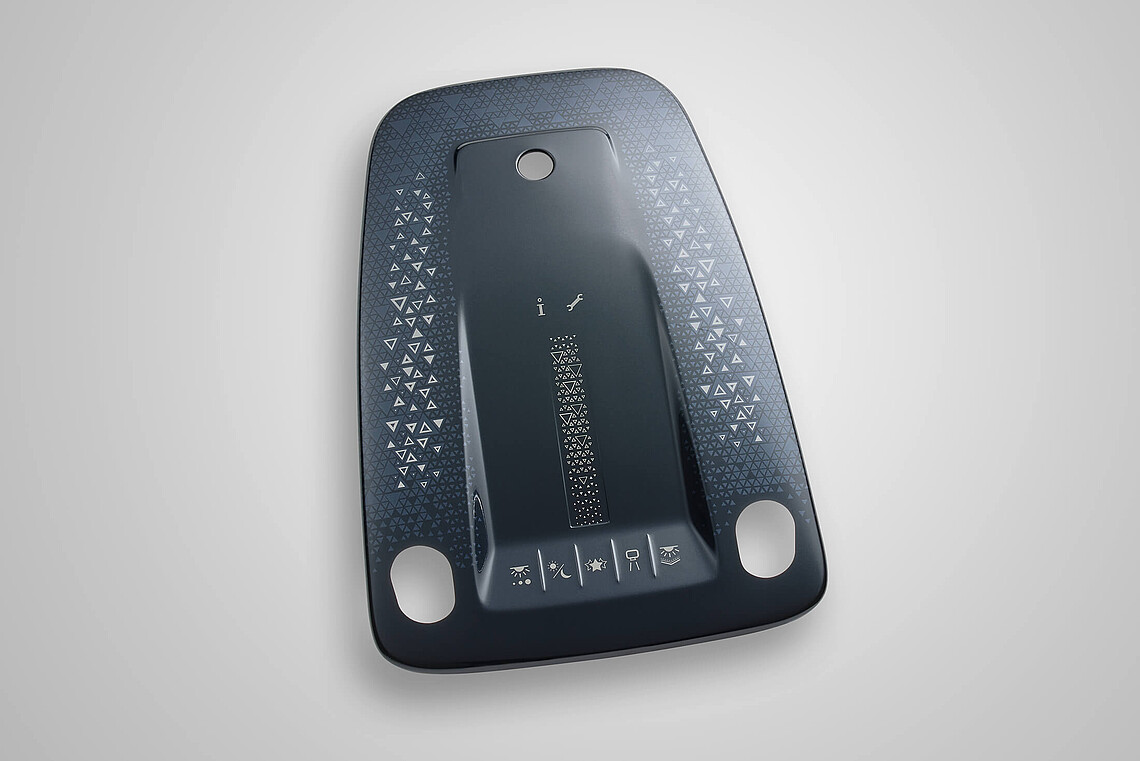


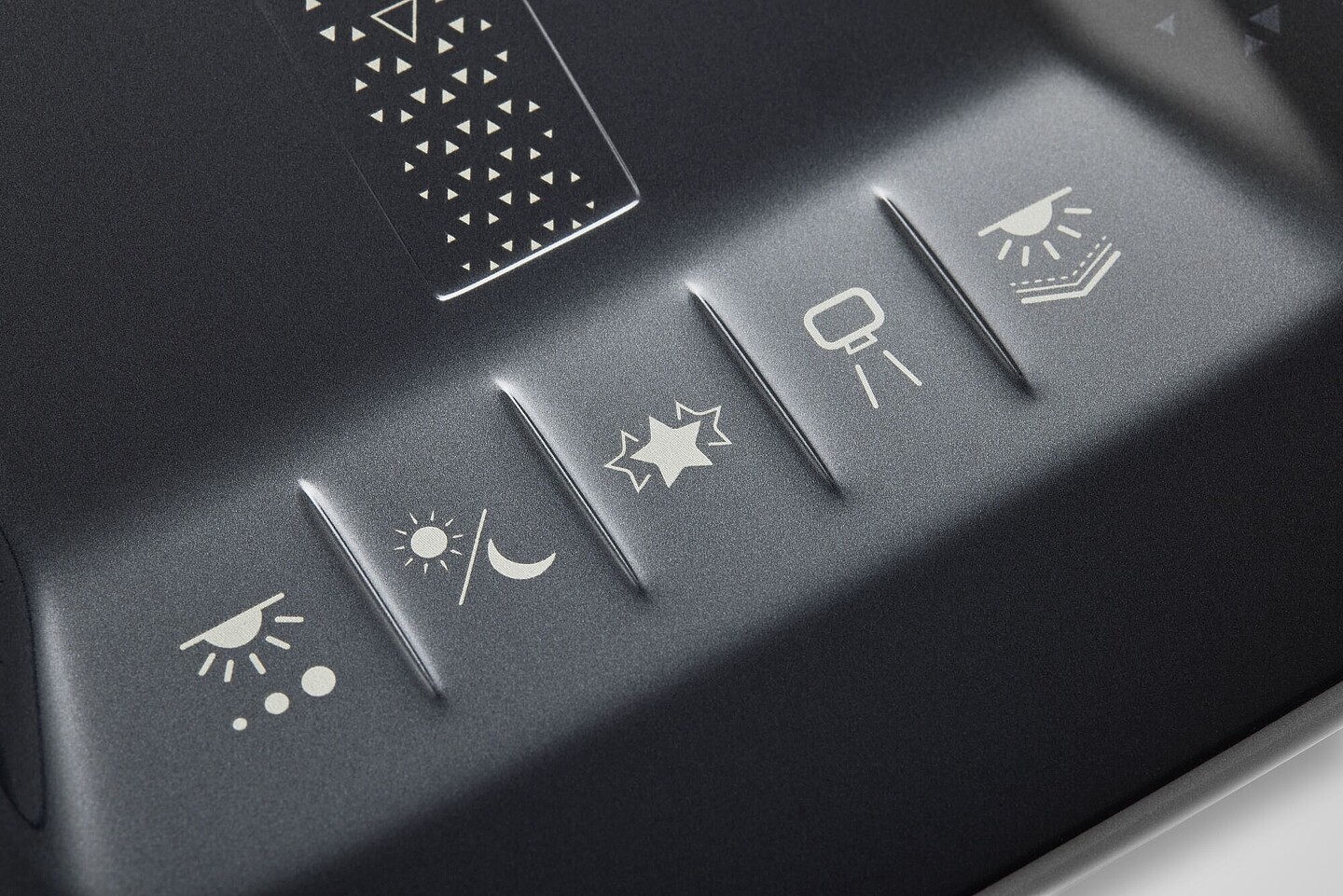
- The innovative overhead console is created using In-Mold Electronics (i.e., an IMD process with simultaneous sensor integration) in a single process step, which saves a lot of CO2. The process enables the production of highly 3D-deformed components. A Wittmann Battenfeld machine of the latest generation is used to manufacture the component. While on one side of the injection mold the carrier material including decorative coating is positioned with light guide sensors by means of a foil-feed device, the capacitive touch sensor (IME label) is inserted into the opposite cavity.
- New: The patented ‘tail to center’ sensor integration from KURZ enables perfect edge decoration of the component beyond the tool edge. The sensor tail is brought to a 45-degree angle to the component via a sliding device in the tool. Thanks to the non-stick coating, it can be positioned precisely on the rear of the component.
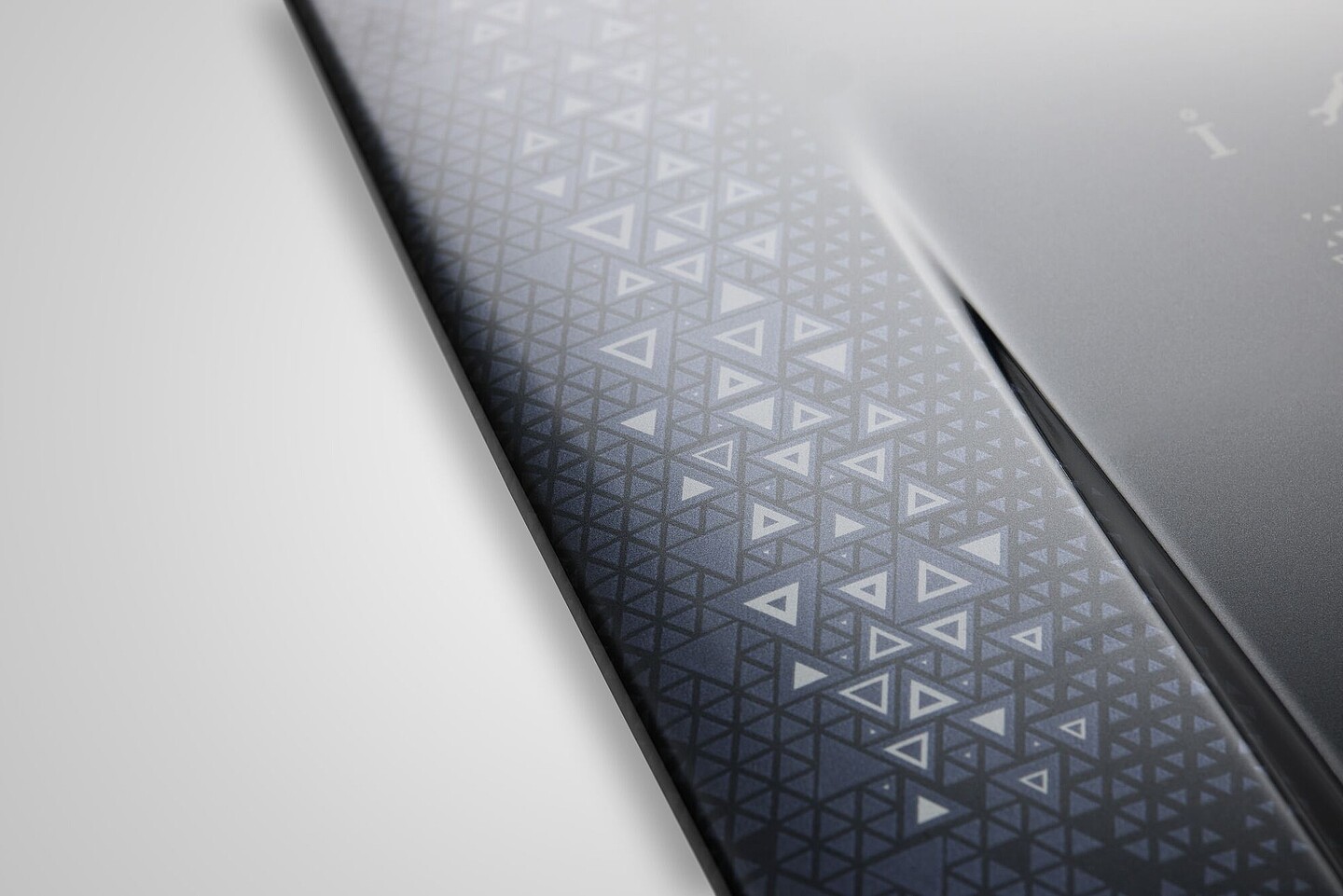
- The PolyTC® sensors come from KURZ subsidiary POLYIC. The extra-thin capacitive sensor films are particularly flexible and robust due to their metal mesh structure. They are thinner than a human hair and do not impair the recyclability of the component.
- The organic shape of the component interface supports intuitive operation of the integrated control elements.
- The tool technology and concept idea come from Syntech Plastics, a plastics specialist and manufacturer of complex components and assemblies.
- Light management and gobo projections were developed by ams Osram Automotive Lighting Systems (AMLS). The cone size of the integrated matrix LED spotlight reading lights in the roof-lining can be adjusted just as individually as the ambient lighting. The built-in logo projector makes it possible to transport individual brand elements to different surfaces inside the vehicle. This function can also be individually adapted.
- BAIER modules take care of CO2 cleaning and UV curing of the finished component directly during the manufacturing process.
Conclusion
Solutions are successful when they are well thought out - from the initial idea to the finished product. KURZ thinks holistically and comes up with patent-ready solutions together with innovative partners and subsidiaries. Intelligent control and attractive design are perfectly implemented in this roof-lining console concept. It shows how modern technologies can replace multiple elements, switches, and controllers with a single, visually appealing component in a sustainable and efficient way. Your benefits: Custom solutions to help you maintain your competitive edge.